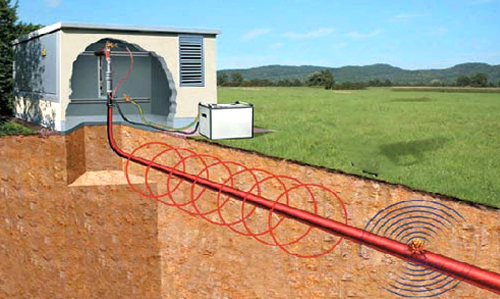
Underground cables are a critical component of modern power distribution networks. Unlike overhead lines, these cables are protected from weather-related damages but are still vulnerable to faults due to aging, insulation failure, water ingress, and mechanical damage. Identifying and diagnosing these faults efficiently is essential to ensuring minimal downtime and reducing maintenance costs. This blog explores the most effective underground cable fault testing and diagnostic techniques, along with best practices for reliable power delivery.
Common Causes of Underground Cable Faults
- Insulation Breakdown: Over time, cable insulation deteriorates due to thermal stress and electrical aging, leading to insulation failure.
- Water Ingress: Water penetration in cable joints and terminations can cause corrosion and insulation degradation.
- Mechanical Damage: Accidental digging, rodent activity, or pressure from heavy vehicles can damage underground cables.
- Overloading: Excessive load can overheat cables, leading to thermal degradation and faults.
- Manufacturing Defects: Poor-quality insulation, conductor defects, or improper cable laying techniques can lead to early failures.
Techniques for Underground Cable Fault Testing & Diagnostics
- Time-Domain Reflectometry (TDR): TDR is a widely used method that sends a low-energy pulse down the cable and measures the reflected signals. Any discontinuities or impedance changes help pinpoint the fault location.
- Very Low Frequency (VLF) Testing: VLF testing is used to assess insulation health in medium and high-voltage cables. It applies a low-frequency AC voltage to detect potential weak points without causing excessive stress.
- Tan Delta Testing: Tan delta testing measures insulation degradation by analyzing dielectric losses in cables. A high tan delta value indicates insulation aging or water treeing.
- Partial Discharge (PD) Testing: PD testing identifies weak insulation spots where electrical discharges occur before a complete breakdown. It is an essential tool for predictive maintenance.
- High-Potential (Hi-Pot) Testing: Hi-Pot testing applies high voltage to cables to check for insulation strength. It helps detect latent defects before a catastrophic failure.
- Fault Locators (Thumpers): A thumper is used to pinpoint underground cable faults by applying a high-energy pulse. It creates an audible thump at the fault location, allowing technicians to locate and repair the fault quickly.
Best Practices for Underground Cable Diagnostics
- Routine Maintenance: Regular inspections and testing help identify potential issues before they escalate.
- Use of Advanced Diagnostics: Combining multiple testing techniques provides a comprehensive view of cable health.
- Proper Cable Installation: Following industry standards during cable laying minimizes future fault occurrences.
- Data Logging & Analysis: Keeping track of test results helps in predictive maintenance and future planning.
- Training & Safety: Skilled personnel and adherence to safety protocols ensure accurate diagnostics and reduced risks.