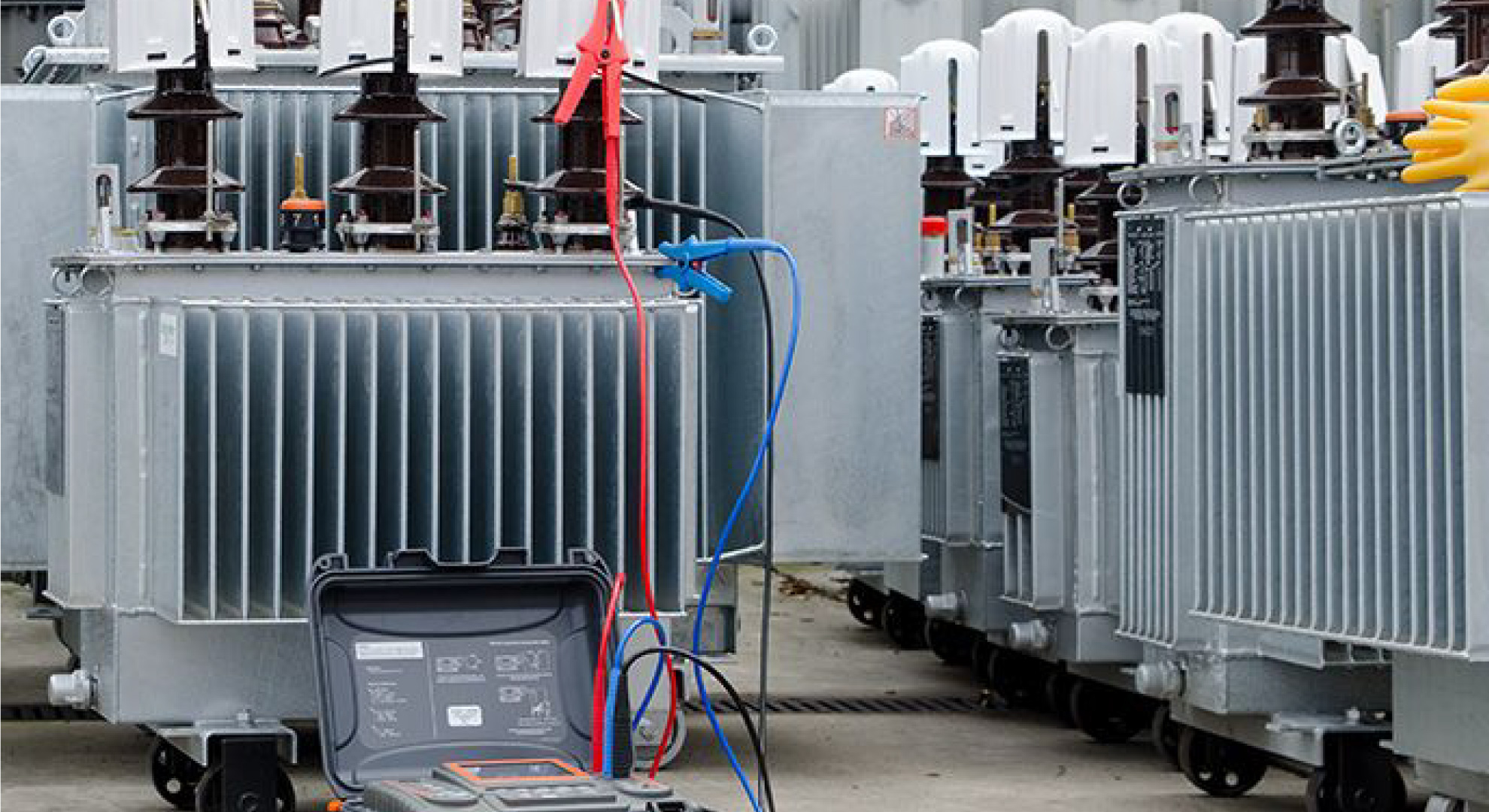
The Insulation Resistance Test is an essential electrical testing technique to evaluate the insulation quality of electrical wires, motors, transformers, and other electrical components. The primary goal of this test is to determine whether the insulation of an electric circuit or component is sufficiently protected and whether any electricity is leaking through it.
This test establishes the efficacy of the device’s insulation and its potentially critical condition. Good insulation resistance means that the device will operate safely and reliably, while poor insulation means there could be residual current leakage, which may increase the risk of latent hazards or accidents. Overall, this test is important to ensure electrical safety.
What is Insulation Resistance Testing?
An insulation resistance test is an electrical test that measures the degree to which the insulations (either absolute, RPM, or protective) of wires, cables, motors, transformers, and other electrical equipment are effective. More simply, this test determines how well the insulation of an item prevents electrical current from leaking.
Common Applications of Insulation Resistance Test
Industrial Applications
- Motor and Generator Testing: To check the condition of the insulation in the motor windings.
- Transformer Insulation Testing: To check whether the insulation between the core and the coil of the transformer is correct.
- Cabling System Check: To determine whether the insulation of large industrial cables is damaged.
- Control Panels and Circuit Breakers: To check whether the electrical panels are safe and functional.
Residential Applications
- House wires: To check whether the insulation of old or new house wires is correct.
- Electrical Device Check: To check whether the insulation of the refrigerator, oven, AC, etc., in the house is good.
- Safety Inspection: To ensure the overall electrical safety of the house.
Commercial Applications
- Installation testing of office buildings: Checking the insulation condition of the computer, AC, and lighting system cables.
- Server rooms and data centers: Insulation checks of high-specification cabling and equipment.
- As part of maintenance work, Insulation resistance tests are performed during regular maintenance.
Equipment Tested
- Cables and Wires: Used to ensure the insulation protects the conductors from leakage.
- Transformers: Checks the insulation between windings and the transformer core.
- Motors: Evaluates the insulation between the windings and the motor frame.
- Switchgear: Verifies the insulation integrity of switches and other high-voltage equipment.
- Other electrical equipment: Used on a wide range of electrical devices and components.
Importance of Insulation Resistance Test
Insulation Resistance Test is an important electrical safety test, which is used to check the condition of the insulation or insulation of electrical wires, equipment and systems. This test can be used to determine how effectively the insulation is able to prevent the flow of electricity.
- Ensures safety: Poor insulation can cause short circuits, fires, or electric shocks. Insulation resistance tests can detect these in advance and allow for preventive measures.
- Increases system reliability: This test helps to ensure that equipment and wires are working properly and the risk of sudden failure is low.
- Simplifies maintenance planning: Regular insulation resistance tests can detect if the insulation of any equipment is weakening in advance so that timely repairs or replacements can be made.
- Legal and industry standards: Insulation testing is mandatory in many industries. It helps to meet various international standards (such as IEC, IEEE).
- Insulation Resistance: Electrical Wire or components insulation designed to prevent the electricity path between the inner conductive part and the outer metal sheath metallic ground. Maintaining electrical system safety, efficiency, and durability is a lot in the trenches of insulation resistance.
- Prevents Accidents: Part of the electrical equipment that is living without its insulation will lead to high-consequence risks, for example, fires. Proper insulation resistance practically nullifies such impending risks.
- Enhances system durability: A good insulation system keeps the power supply system usable for a longer time. It allows the equipment to operate long time in good condition.
- Faster maintenance: If you perform insulation resistance testing on a regular basis, it’s easier for the maintenance crews to figure out what equipment or wire is failing and replace or repair it.
- Enhances commercial and industrial reliability: Insulation resistance testing is crucial to maintaining generated power of a factory or office. This helps in minimizing enzymatic breakdowns and the loss of production.
- Reduces business losses: Production can be halted if equipment breaks down. Identifying risks through insulation testing in advance can reduce such unexpected losses.
Tools and Equipment Used
- Test leads and probes: By using either an AC megohmmeter instrument connected to both ends of the test circuit or a cable in various types of leads & probes.
- Worn Insulated Gloves: To be used while doing a safety test. Wear Safety Gloves . Poper Eye Protection, Such as When Working on High Voltage Circuits
- Lotus Work Order: Lockout/Tagout and signs to prevent anyone from turning on the circuit while working.
- Multimeter Type: Used to ascertain whether or not the circuit in question is live ;hwever, this is not an indirect measure of insulation resistance.
- Insulation Resistance Test Report Form/ Software: Result is recorded in form of a report or some digital software.
Common Problems and Troubleshooting
The Insulation Resistance Test is an important electrical test that is used to determine whether the insulation of wires, cables, equipment, and machines is in good condition. However, various problems can occur in this test. Below are some common problems and their solutions:
Low resistance readings are obtained
- Insulation is old or damaged
- Moisture (wet) on the cable or device
- Dirt, dust, or oil buildup
- The testing device is not connected properly
Reading shows zero or infinity
- Disconnected
- A wire in the tester device is open
- Open circuit in the device or wire
- Short circuit inside the device
Readings fluctuate
- High humidity or heat in the environment
- Leakage current in the machine
- Probe or clamp not installed correctly
Troubleshooting Instructions
Before Testing:
- Make sure all wires and equipment are clean and dry.
- Verify that the insulation resistance meter is calibrated.
- Check that the connections are secure before testing.
If a problem occurs:
- If the reading is too low, the insulation may be bad — replace the wire or equipment.
- If the insulation is bad, repeat the test using a drying method (heater, hot air gun, etc.).
- If the tester does not work, check the battery or fuse.
- If the reading fluctuates, reconnect the device and retest.