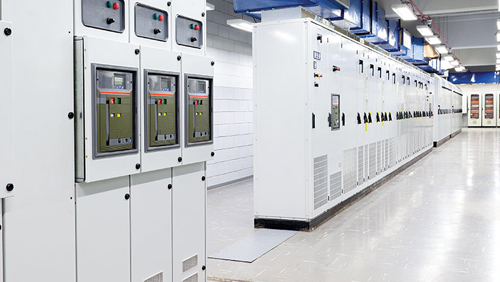
Switchgear is a crucial component in electrical power systems, responsible for controlling, protecting, and isolating electrical equipment. Proper protection and testing of switchgear ensure safety, reliability, and efficiency in power distribution networks. Without proper testing, faults can lead to catastrophic failures, causing downtime, equipment damage, or even hazardous incidents. In this blog, we will explore the importance of switchgear protection testing, its key methods, and best practices for optimal performance.
What is Switchgear Protection Testing?
Switchgear protection testing is the process of evaluating the performance of circuit breakers, relays, and other protective devices to ensure they function correctly during fault conditions. The goal is to prevent electrical failures, minimize risks, and maintain the integrity of the power system.
Importance of Switchgear Protection Testing
- Ensures Safety: Proper testing prevents electrical hazards, protecting personnel and equipment.
- Improves Reliability: Regular testing minimizes the risk of unexpected failures and ensures uninterrupted operations.
- Compliance with Standards: Many industries require adherence to safety regulations and standards, such as IEC, ANSI, and IEEE.
- Reduces Downtime: Early detection of potential issues helps in preventing costly outages.
- Enhances Equipment Lifespan: Identifying faults early reduces wear and tear, extending the life of switchgear components.
Key Methods of Switchgear Protection Testing
- Primary Injection Testing: Primary injection testing involves applying high current to the primary side of the circuit breaker to assess its performance. This test verifies the overall functionality of the switchgear and detects faults in the circuit.
- Secondary Injection Testing: This test is performed on protective relays and control circuits without applying high voltage to the primary circuit. It ensures that relays and trip units respond correctly to electrical faults.
- Contact Resistance Testing: This test measures the resistance of circuit breaker contacts to ensure minimal energy loss and efficient current flow. High resistance can indicate wear, corrosion, or loose connections.
- Insulation Resistance Testing: By applying a high voltage to measure the insulation resistance, this test ensures that insulation materials prevent leakage currents and breakdowns.
- Circuit Breaker Timing Test: This test measures the opening and closing times of circuit breakers to ensure they operate within the required limits for fault clearing.
- Partial Discharge Testing: Detecting and measuring partial discharges in insulation materials helps in preventing electrical breakdowns and extending equipment life.
Best Practices for Effective Switchgear Protection Testing
- Follow Manufacturer Guidelines: Always refer to the switchgear manufacturer’s specifications for recommended testing procedures.
- Use Certified Testing Equipment: Ensure that the test instruments comply with industry standards for accuracy and reliability.
- Schedule Regular Maintenance: Implement a preventive maintenance program to test switchgear at recommended intervals.
- Train Personnel: Skilled technicians should perform testing to ensure accurate results and proper handling of equipment.
- Document Test Results: Keeping detailed records helps in trend analysis and proactive decision-making.
- Adopt Predictive Maintenance: Utilize modern diagnostic tools to anticipate failures before they occur.