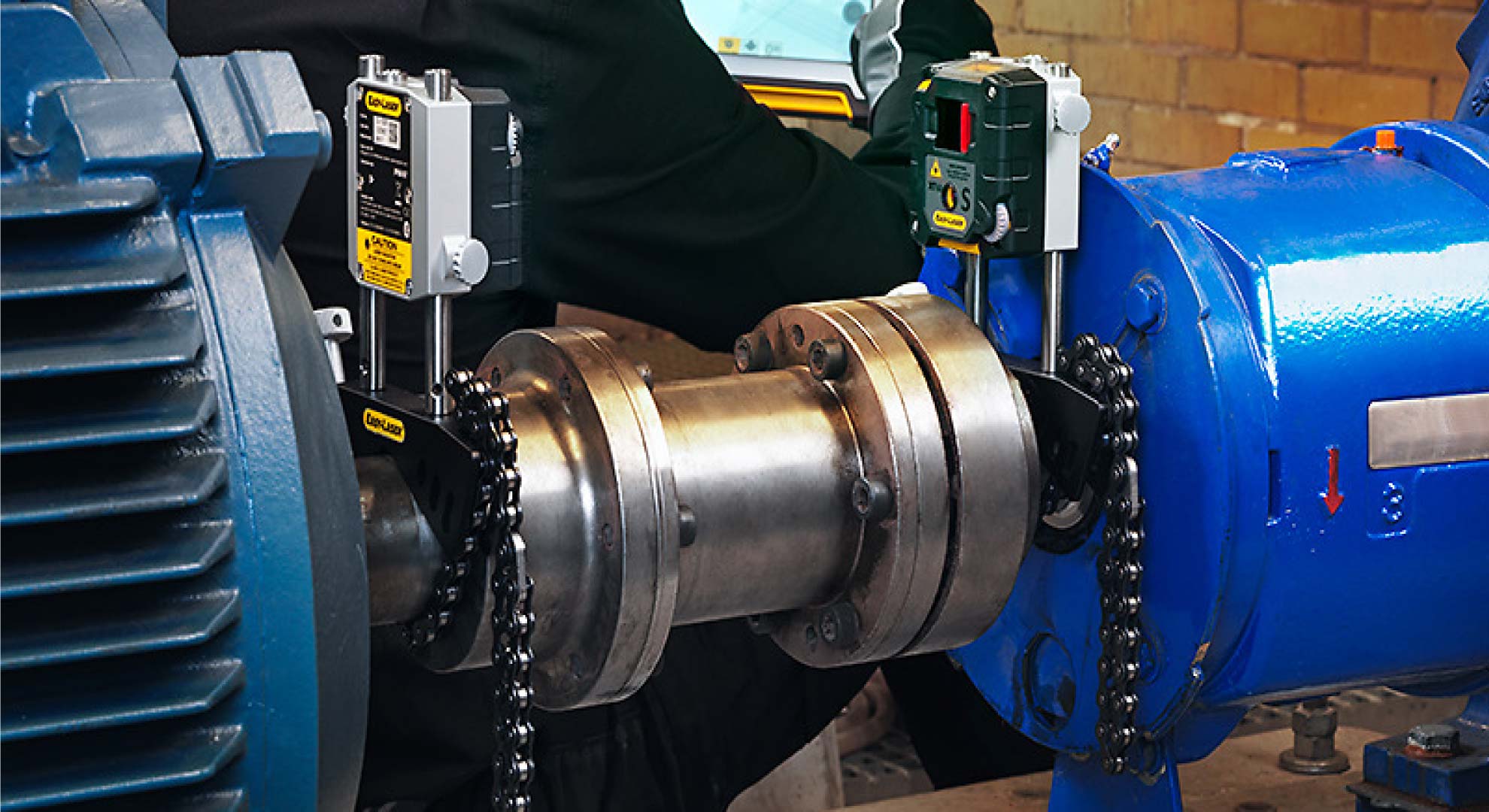
With the advancement of technology, proper and efficient management has become very important in various fields. Especially in the case of machinery or mechanical systems, it is necessary to ensure the functionality of each part. And a special method called “Precision Equipment Modeling System” (PEMS) helps in doing that. It is a state-of-the-art technology that creates accurate models of machinery or systems to analyze and improve their performance. Let’s know how this system works and its importance.
What is Precision Equipment Modeling System?
Precision Equipment Modeling System (PEMS) is a technology that creates an accurate and precise model at all stages of the design, production and use of machinery. Through this system, it is possible to analyze the movement, energy consumption, temperature, pressure, etc. of each part of the machinery. Basically, it is used to improve the design of machinery and ensure long-term performance.
How does PEMS work?
The PEMS system mainly works through various types of sensors and data analysis technologies. This technology collects accurate information depending on the performance and situation of the equipment, which helps in the design or modeling process. It uses special software that analyzes the parameters accurately. It identifies equipment faults through modeling, provides improvement suggestions, and provides appropriate suggestions to increase performance.
Benefits of PEMS:
- Increase efficiency:
The PEMS system helps improve the performance of the equipment. Through this, it is possible to predict the condition and results of the equipment, which reduces operational costs. - Identify potential faults:
By analyzing the activities of each part of the equipment, potential faults or failures can be identified in advance, which can prevent failures and reduce accidents. - Save time and cost:
By identifying equipment problems, waste of time and cost can be prevented. Through this, continuous work can be done, and more work can be done in less time. - Analytical decision-making:
This system can analyze various parameters, which makes it easier to make the right decisions about the production process or equipment design.
PEMS application areas:
Precision Equipment Modeling System can be used in various fields. It is especially used in automobiles, aerospace technology, power plants, industrial equipment and laboratories. In the automobile industry, the performance and safety of the vehicle is increased by creating accurate models of each part of the equipment. In addition, this system is also used in aerospace technology, where highly accurate and precise equipment is required.
Precision Equipment Modeling System is a very important technology, which helps to ensure the correct functioning and improvement of equipment. Through this, it is possible to ensure accuracy, efficiency, and cost-effectiveness, which are essential for future industries and technologies.