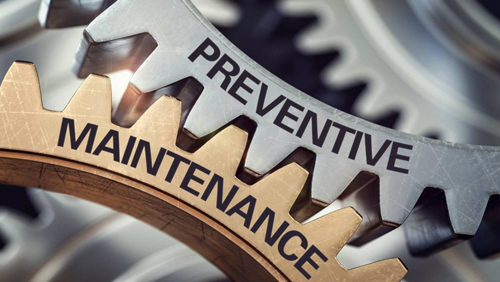
Mechanical preventive maintenance is a crucial practice that ensures the longevity, efficiency, and reliability of machines and equipment. Businesses that rely on mechanical systems must adopt a preventive approach rather than reactive maintenance to reduce downtime, enhance safety, and optimize performance. This guide explores the importance of preventive maintenance, key strategies, and the long-term benefits of implementing a structured maintenance plan.
What is Mechanical Preventive Maintenance?
Mechanical preventive maintenance (PM) refers to scheduled inspections, servicing, and repairs of machinery to prevent unexpected breakdowns. This approach minimizes costly repairs and ensures that equipment runs at peak efficiency. Unlike reactive maintenance, which deals with fixing issues after they occur, PM proactively prevents failures.
Benefits of Mechanical Preventive Maintenance
- Increases Equipment Lifespan
Routine maintenance helps prevent wear and tear, significantly extending the life of mechanical components. - Reduces Downtime & Productivity Loss
Unplanned equipment failure can halt operations, leading to productivity and revenue losses. Preventive maintenance minimizes such risks. - Enhances Safety
Well-maintained machinery reduces the chances of accidents and workplace injuries caused by equipment failures. - Reduces Repair Costs
Fixing minor issues early is more cost-effective than addressing major breakdowns, which often require expensive repairs or replacements. - Improves Energy Efficiency
Properly maintained equipment operates more efficiently, reducing energy consumption and lowering utility costs. - Ensures Compliance with Industry Standards
Many industries have regulations requiring regular maintenance to ensure safety and performance compliance.
Key Components of a Preventive Maintenance Plan
- Regular Inspections & Monitoring
- Conduct routine checks to detect early signs of wear and tear.
- Use predictive maintenance tools like vibration analysis and infrared thermography to anticipate failures.
- Scheduled Servicing & Lubrication
- Follow manufacturer-recommended servicing schedules.
- Ensure moving parts are properly lubricated to reduce friction and wear.
- Parts Replacement & Upgrades
- Replace worn-out components before they fail.
- Upgrade machinery with newer, more efficient parts when possible.
- Training & Skill Development
- Train maintenance personnel to identify issues and perform routine servicing.
- Educate operators on proper equipment handling to prevent misuse.
- Record-Keeping & Documentation
- Maintain logs of maintenance activities to track performance trends.
- Use computerized maintenance management systems (CMMS) to streamline scheduling and record-keeping.
Common Mechanical Systems That Require Preventive Maintenance
- HVAC Systems – Regular filter replacements and duct cleaning prevent inefficiency.
- Pumps & Motors – Lubrication and alignment checks prevent overheating and damage.
- Conveyors & Bearings – Routine inspections prevent misalignment and breakdowns.
- Hydraulic Systems – Fluid checks and seal replacements ensure smooth operation.
Mechanical preventive maintenance is a proactive approach that saves businesses time, money, and resources while ensuring operational efficiency. A well-planned maintenance strategy enhances safety, extends equipment life, and improves overall productivity. Investing in a structured PM program ultimately leads to long-term success and cost savings. Start implementing a robust preventive maintenance plan today to ensure your mechanical systems operate at their best.