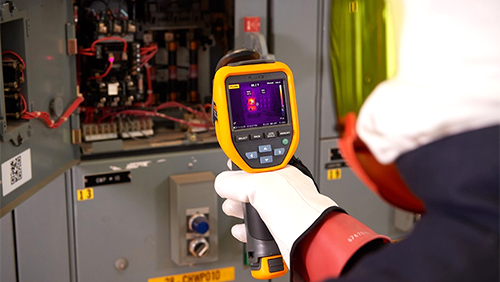
Electrical systems are the backbone of modern infrastructure. Whether in homes, industries, or commercial buildings, reliable electrical systems are essential for safety, efficiency, and productivity. Electrical Preventive Maintenance (EPM) is the proactive approach to maintaining electrical components before failures occur. This blog will explore the importance of EPM, its benefits, and best practices for an effective maintenance program.
What Is Electrical Preventive Maintenance?
Electrical Preventive Maintenance (EPM) refers to regular inspection, testing, and servicing of electrical equipment to prevent failures, improve efficiency, and extend equipment lifespan. Unlike corrective maintenance, which fixes issues after failure, EPM ensures problems are identified and addressed before they cause costly disruptions.
Importance of Electrical Preventive Maintenance
- Prevents Unexpected Downtime – Electrical failures can halt operations, leading to financial losses. Routine maintenance minimizes the risk of unexpected failures.
- Ensures Safety – Faulty electrical systems pose fire hazards and electrocution risks. EPM enhances workplace and residential safety.
- Increases Equipment Lifespan – Regular maintenance reduces wear and tear, keeping electrical components in optimal condition for longer.
- Reduces Repair Costs – Preventive measures cost less than emergency repairs or equipment replacements.
- Enhances Energy Efficiency – Proper maintenance ensures that electrical systems operate efficiently, reducing energy waste.
- Compliance with Regulations – Many industries have legal requirements for electrical maintenance to ensure safety and operational reliability.
Key Components of an Electrical Preventive Maintenance Program
- Regular Inspections
- Visual checks for overheating, corrosion, or physical damage.
- Identifying loose connections or exposed wiring.
- Thermal Imaging
- Infrared scans detect overheating components before failure occurs.
- Cleaning and Lubrication
- Dust and debris can cause overheating and equipment failure.
- Lubricating moving parts prevents friction-related damage.
- Voltage and Current Testing
- Identifying overloading or imbalanced loads to prevent overheating.
- Measuring voltage drops and correcting issues.
- Testing Circuit Breakers and Fuses
- Ensuring proper operation and replacing faulty components.
- Inspecting Transformers and Capacitors
- Checking for leaks, insulation breakdown, and performance efficiency.
- Updating Electrical Panels
- Ensuring panels are up-to-date to handle load requirements.
- Maintaining Backup Systems
- Testing generators and UPS systems to ensure readiness during power failures.
Best Practices for Effective Electrical Preventive Maintenance
- Develop a Maintenance Schedule – Set up a routine maintenance schedule based on manufacturer recommendations and industry standards.
- Train Personnel – Ensure staff is trained in electrical safety and maintenance protocols.
- Use Advanced Diagnostic Tools – Thermal cameras, power quality analyzers, and other tools can help detect potential issues early.
- Keep Maintenance Records – Documenting inspections and repairs helps track trends and identify recurring issues.
- Follow Safety Standards – Adhere to OSHA, NFPA 70E, and other safety guidelines.
- Partner with Experts – Hire certified electricians and maintenance professionals for specialized tasks.
- Plan for Emergencies – Have contingency plans in place for power failures or major repairs.