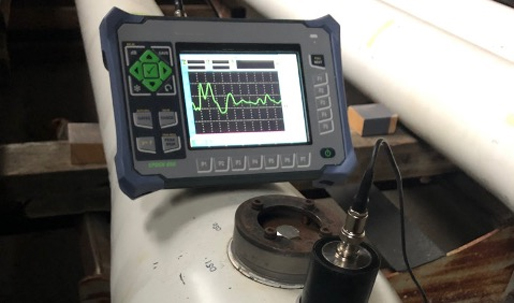
In the ever-evolving world of roads and transportation infrastructure, ensuring safety, durability, and performance is critical. Composite materials have become increasingly popular due to their strength, lightweight properties, and resistance to environmental factors. However, these materials are not immune to flaws that can compromise their effectiveness. Detecting these flaws early is essential to maintain infrastructure integrity and minimize repair costs. In this blog, we delve into the importance of composite flaw detection in roads and transportation systems and how advanced technologies help prevent accidents and ensure long-lasting infrastructure.
What are Composite Materials in Roads & Transportation?
Composite materials are engineered materials made from two or more distinct substances, resulting in superior performance characteristics. In the context of roads and transportation, composites are often used in:
-
Pavement materials: For stronger and more durable road surfaces.
-
Bridges: Lightweight yet highly durable materials for construction.
-
Railways: High-performance materials in track components and supports.
-
Vehicles: Lightweight materials for fuel-efficient designs.
These materials offer significant advantages, such as resistance to corrosion, a high strength-to-weight ratio, and a longer lifespan. However, these benefits can be undermined if flaws such as cracks, delaminations, or fatigue failures are not detected in time.
Why is Flaw Detection Crucial in Roads & Transportation?
Flaw detection in composite materials is crucial for several reasons:
-
Safety: Flaws in composite materials can lead to structural failures, accidents, and even fatalities. Early detection helps mitigate these risks and prevent catastrophic incidents.
-
Cost Efficiency: Detecting flaws early reduces maintenance and repair costs by addressing problems before they escalate.
-
Longevity: Timely detection and maintenance ensure the longevity of infrastructure, reducing the need for costly replacements.
-
Compliance: Regular flaw detection helps infrastructure meet safety and regulatory standards, avoiding potential legal or insurance-related issues.
Advanced Technologies for Composite Flaw Detection
The detection of flaws in composite materials requires precise and non-invasive technologies. Several cutting-edge methods are available for road and transportation engineers to identify flaws early:
-
Ultrasonic Testing (UT): Ultrasonic testing uses high-frequency sound waves to detect internal flaws in composite materials. By analyzing how sound waves travel through the material, engineers can identify areas of weakness, such as delaminations, cracks, and voids that might not be visible to the naked eye.
-
Infrared Thermography (IRT): Infrared thermography is a non-destructive testing technique that detects temperature differences on the surface of composite materials. When flaws such as delaminations or air pockets are present, they affect heat conduction, resulting in thermal anomalies. This method is ideal for large surface areas, like roadways or bridge decks.
-
Acoustic Emission Testing (AE): Acoustic emission testing detects high-frequency sound waves emitted by cracks or other flaws in materials. This technique is used to monitor live systems under stress, allowing for real-time detection of potential failures in road and transportation structures.
-
X-ray and CT Scanning: X-ray and computed tomography (CT) scanning offer high-resolution imaging of composite materials. These methods provide a 3D view of the internal structure, allowing engineers to spot flaws that could compromise the material’s strength and stability.
-
Drone and Remote Sensing Technologies: Drones equipped with high-resolution cameras and sensors are increasingly used for road and bridge inspections. These unmanned aerial vehicles can quickly scan large areas, capturing detailed images and data that can be analyzed for any potential flaws in the composite materials.
-
Machine Learning and AI for Predictive Analysis: Artificial Intelligence (AI) and machine learning algorithms can be integrated with flaw detection systems to predict potential weaknesses based on historical data and real-time monitoring. These technologies can optimize maintenance schedules, ensuring that any flaws are addressed before they lead to failure.
Benefits of Composite Flaw Detection in Roads & Transportation
-
Enhanced Safety: By detecting flaws in composite materials early, engineers can perform timely repairs, ensuring safer travel for vehicles and pedestrians alike. This is especially critical in transportation systems where high-speed traffic and heavy loads are involved.
-
Improved Durability: Regular flaw detection extends the lifespan of roads, bridges, and other transportation infrastructure, reducing the need for frequent repairs or replacements and optimizing the lifecycle of these assets.
-
Cost Savings: Preventive maintenance through early detection of flaws can significantly reduce the cost of repairs. By addressing minor issues before they escalate into major failures, transportation authorities can save on the high costs of emergency repairs and replacements.
-
Environmental Sustainability: Detecting flaws in composite materials allows for more efficient resource use and less waste. By maintaining existing infrastructure rather than replacing it, cities and governments can reduce the environmental impact associated with the construction of new roads and transportation systems.