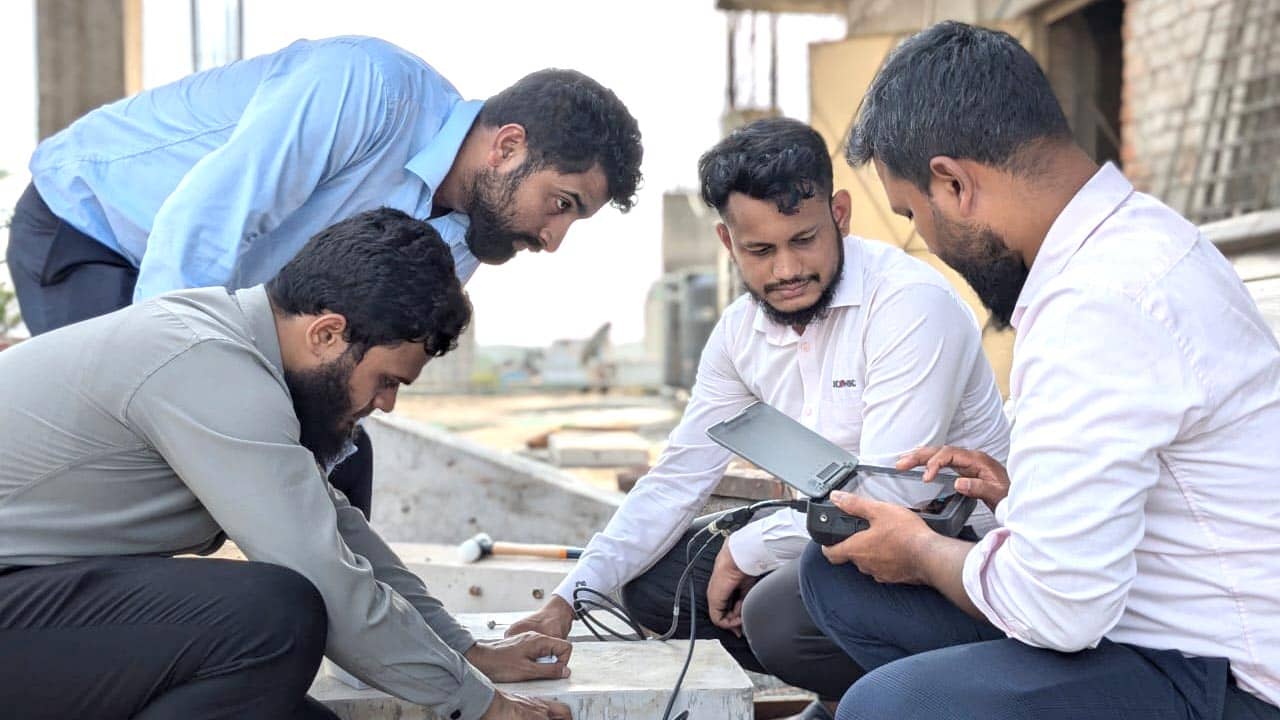
Bangladesh has made significant strides in its journey towards development and prosperity. The initial phase, known as “Digital Bangladesh,” focused on leveraging information and communication technology to drive economic growth and improve the quality of life for its citizens. Building on this foundation, the country is now transitioning towards “Smart Bangladesh,” encapsulated in Vision 2041, which aims to transform Bangladesh into a high-income and developed nation by 2041.
Sustainability at the Core
Central to Vision 2041 is sustainability. Ensuring long-term economic, social, and environmental sustainability is crucial for achieving the ambitious goals outlined in this vision. To this end, quality assurance across various sectors becomes paramount. High standards of quality are essential for sustaining growth, fostering innovation, and maintaining competitiveness on a global scale.
Enhancing Quality Assurance through Testing and Calibration
Bangladesh has now reached a peak to transform its infrastructure. For a developed nation it is important to have a developed facility for testing & research. To ensure superior quality in products, services, and infrastructure, it is imperative to develop robust testing and calibration facilities. ICONIC Engineering Ltd. has its in-house facility as an accredited Calibration Service Provider in Bangladesh. These facilities play a vital role in maintaining standards, ensuring safety, enhancing reliability, and regular commissioning. Regular maintenance and check-ups of infrastructure and equipment are essential components of this process, helping to identify and rectify potential issues before they become significant problems.
Regular maintenance and check-ups of infrastructure and equipment, conducted in collaboration with the Local Government Engineering Department (LGED), Public Works Department (PWD), Roads & Highway Department (RHD), Bridge Authority, and City Corporation, help identify and rectify potential issues before they escalate. As key stakeholders, these departments rely on ICONIC Engineering Ltd.’s advanced technology and expertise to ensure the highest quality standards are met.
As we know we are proudly stepping into Digital Bangladesh and Focusing on driving into Smart Bangladesh. For a Smart Nation, Sustainability is a must. To acquire its potential
sustainability Quality assurance is the focal point for every segment. If we focus on getting the best quality among our resources Testing Facility is a must. ICONIC Engineering Ltd. has built up its capacity for Introducing Global Technologies with its local expertise in Bangladesh.
How ICONIC is focused on 3M
For every Smart Vision 3M is a must which reflects Man, Machine, and Method. ICONIC Engineering Ltd. is focused on providing world-class machines & Equipment driven from any part of the world. They will develop these global technologies through world-class training provided to consumers with their local expertise. The local knowledge will develop the best method to drive the Machines. Once the method for driving the machine is developed, it’ll automatically develop its Man, which is the focus for Building a “Smart Vision”.
Non-Destructive Testing (NDT) in civil engineering refers to a range of analysis techniques used to evaluate the properties of a material, component, or system without causing damage. These tests are essential for assessing the integrity and safety of structures such as buildings, bridges, dams, and other infrastructure. The primary goal of NDT is to detect defects and irregularities, measure material properties, and ensure that structures comply with safety standards without compromising their usability. ICONIC Engineering Ltd., with over a decade of experience, offers a comprehensive range of NDT services to meet this demand.
The global NDT market size was valued at approximately USD 19 billion in 2020 and is projected to reach over USD 30 billion by 2027, growing at a compound annual growth rate (CAGR) of around 8%.
ICONIC Engineering Ltd., with over a decade of experience, offers a comprehensive range of NDT services to meet this demand. The similar tests are listed below broadly:
Compressive Strength Test of Concrete
Concrete as a building material has ancient roots, but the development of Portland cement in the early 19th century by Joseph Aspdin, an English mason, marked the beginning of modern concrete. The need to test its strength became apparent as its use in construction expanded.
The compressive strength test measures the maximum load a concrete specimen can bear before it fails under compression. Among these methods, the rebound hammer test is widely used for its simplicity and effectiveness.
For instance, market reports have estimated the global concrete testing market to be valued at over $500 million, with expectations for steady growth in the coming years. This market includes various testing services such as compressive strength, durability, and material composition testing
The compressive strength of concrete is a key indicator of its ability to withstand loads and stresses. This is traditionally determined through destructive testing methods involving breaking concrete specimens. However, NDT methods provide a non-invasive alternative.
Test Procedure with Rebound Hammer:
The Rebound Hammer, also known as the Schmidt Hammer, was first introduced in 1954 by Ernst Schmidt, a Swiss engineer. This device is used to assess the compressive strength of concrete and rock by measuring the rebound of a spring-loaded mass impacting the surface, and measuring the surface hardness of concrete, which correlates with its compressive strength. Here’s a basic procedure for conducting the rebound hammer test:
- Preparation: Ensure the concrete surface is clean and free from loose particles or debris.
- Calibration: Calibrate the rebound hammer with an anvil according to the manufacturer’s instructions to ensure accurate results.
- Testing: Perform the following steps:
- Hold the rebound hammer perpendicular to the concrete surface being tested.
- Press the hammer against the surface and trigger the release mechanism.
- Note the rebound value indicated on the hammer’s scale.
- Recording: Record multiple readings at different locations on the concrete surface to account for variations in hardness.
- Correlation: Use the rebound values to estimate the compressive strength of concrete based on empirical correlations provided by the rebound hammer manufacturer.
Advantages of Rebound Hammer
- Non-destructive: Does not damage the concrete surface or require the removal of samples.
- Portable: Easy to transport and use on-site, making it suitable for field testing.
- Quick Results: Provides immediate results, allowing for rapid assessment of concrete strength.
- Cost-effective: Compared to traditional destructive tests, rebound hammer testing is relatively inexpensive.
- Software Driven: Its results are averaged through automated software.
Table showing some short parameters:
Aspect | Description |
Test Method | Compressive Strength Test using Rebound Hammer |
Purpose | Estimate concrete compressive strength based on rebound hardness measurements |
Equipment | Schmidt Rebound Hammer or similar |
Advantages | Non-destructive, quick, suitable for in-situ and lab testing |
Limitations | Surface sensitivity, affected by conditions like moisture, less precise than other methods |
Common Failures for Not Using Rebound Hammer:
- Inaccurate Strength Assessment: Misses estimating concrete compressive strength accurately.
- Missed Weak Areas: Fails to identify critical weak spots in concrete.
- Lack of Quality Control: Results in poor monitoring of concrete quality during construction.
- Limited Decision Data: Prevents informed decisions about concrete strength and maintenance.
- Increased Risk: Raises the risk of structural failure and safety hazards.
- Non-compliance: Fails to meet industry standards and regulatory requirements.
- Difficulty in Defect Detection: Makes it hard to detect cracks and other defects early on.
Using rebound hammers correctly ensures accurate assessments and enhances structural integrity and safety.
International Standards
The rebound hammer test is governed by international standards to ensure consistency and reliability in concrete strength assessment. Some relevant standards include:
- ASTM C805: To assess the uniformity of concrete in a structure and estimate its compressive strength by measuring the rebound of a spring-driven mass against the concrete surface
- BS EN 12504-2: To assess the uniformity and quality of concrete and to estimate its compressive strength using the rebound hammer method.
Future Scopes Using Rebound Hammer Technology
The future of rebound hammer technology in concrete assessment looks promising with ongoing advancements:
- Improved Accuracy: Development of more accurate correlations between rebound values and actual compressive strength.
- Integration with Digital Tools: Integration with digital platforms and mobile applications for real-time data analysis and reporting.
- Enhanced Portability and Durability: Continued improvements in the design and materials of rebound hammers for increased reliability and durability.
- Automation and AI: Application of artificial intelligence (AI) and machine learning algorithms for automated data interpretation and predictive analytics.
Regular maintenance of infrastructure, done in partnership with LGED, PWD, RHD, the Bridge Authority, and the City Corporation, helps catch problems early. These organizations trust ICONIC Engineering Ltd. for the latest solutions and expertise to maintain top quality.
Concrete Uniformity Mapping
Concrete uniformity mapping assesses the homogeneity of concrete throughout a structure Concrete uniformity mapping is a critical aspect of quality assessment in construction and maintenance projects. Non-destructive testing (NDT) methods such as the Rebound Hammer and Ultrasonic Pulse Velocity (UPV) device play pivotal roles in evaluating concrete uniformity without causing damage.
In the early 1900s, Duff A. Abrams, an American researcher, significantly influenced concrete technology. He introduced the concept of the water-cement ratio, which is critical for achieving uniform concrete strength and durability.
American Concrete Institute (ACI) founded in 1904, the ACI has been instrumental in promoting standards and guidelines for concrete construction, including uniformity in concrete mixtures.
Portland Cement Association (PCA) was established in 1916, the PCA has also contributed to research and development in concrete technology, emphasizing quality control and uniformity.
Concrete uniformity mapping involves assessing the consistency of concrete properties, including strength and homogeneity, across a structure. This helps identify areas that may require further investigation or remedial actions to ensure structural integrity.
As of recent reports, the global market for concrete testing and inspection services, including uniformity mapping, is growing, with estimates ranging from a few hundred million to over a billion dollars annually.
Test Procedures with Rebound Hammer and Ultrasonic Pulse Velocity:
Rebound Hammer Test Procedure:
- Preparation: Ensure the concrete surface is clean and prepared for testing.
- Calibration: Calibrate the rebound hammer according to manufacturer guidelines to ensure accurate results.
- Testing: Perform the following steps:
-
- Hold the rebound hammer perpendicular to the concrete surface.
- Apply the hammer to the surface and trigger the release mechanism.
- Record the rebound value displayed on the hammer’s scale.
- Repeat at multiple locations to map out concrete uniformity.
Ultrasonic Pulse Velocity (UPV) Test Procedure:
- Preparation: Apply coupling agent to ensure good contact between the transducers and the concrete surface.
- Setup: Place transducers at specified locations on the concrete surface.
- Testing: Transmit ultrasonic pulses through the concrete and record the time for pulses to travel between transducers.
- Calculate the pulse velocity using the distance between transducers and the travel time of the pulse.
- Higher velocities indicate higher concrete density and uniformity.
Advantages of Rebound Hammer and UPV Device
Rebound Hammer:
- Non-destructive: Does not damage the concrete surface.
- Portable: Suitable for field use, providing immediate results.
- Cost-effective: Compared to destructive methods, rebound hammer testing is economical.
Ultrasonic Pulse Velocity Device:
- Accuracy: Provides precise measurements of concrete density and uniformity.
- Operation: UPV is Operated with the SONREB method to get the original data. It can assess the homogeneity of concrete with actual accuracy.
- Speed: Quickly assesses large areas of concrete.
- Versatility: Suitable for various concrete types and conditions.
Table showing some short parameters:
Aspect | Description |
Purpose | Assess the uniformity of concrete properties across a structure or surface |
Methods | Utilizes tools like Rebound Hammer and Ultrasonic Pulse Velocity for non-destructive testing |
Advantages | Identifies variations early, helps in quality control, guides targeted repairs |
Limitations | Surface sensitivity, affected by conditions like moisture, less precise than other methods |
Common Failures:
- Variations in Strength: Some areas may have lower strength, compromising structural integrity.
- Durability Issues: Uneven composition leads to premature deterioration.
- Cracking and Bonding Problems: Increased risk of cracks and poor adhesion between layers.
- Aesthetic and Functional Defects: Inconsistent appearance and potential functional issues.
- Delays and Costs: Remedial work increases project timelines and expenses.
- Non-compliance: Failure to meet standards may lead to regulatory issues.
Early detection through quality control and NDT is crucial for preventing these issues in construction.
International Standards
These testing methods are guided by international standards to ensure reliability and consistency:
- ASTM C805: Standard Test Method for Rebound Number of Hardened Concrete.
- ASTM C597: Provides guidelines for using ultrasonic pulse velocity to evaluate the quality and uniformity of concrete. This test is useful for detecting voids, cracks, and other imperfections within the concrete.
Future Scopes Using These Technologies
The future of concrete uniformity mapping with rebound hammer and UPV technologies holds significant promise:
- Integration with Digital Platforms: Data integration with digital tools for real-time analysis and reporting.
- Advancements in Sensor Technology: Improved sensor capabilities for enhanced accuracy and reliability.
- Automation and AI: Application of artificial intelligence for automated data interpretation and predictive analytics.
- Environmental Adaptability: Development of devices that can operate effectively in diverse environmental conditions.
Regular maintenance and inspections of infrastructure and equipment are critical to preventing issues from escalating. Collaborations with key stakeholders such as the Local Government Engineering Department (LGED), Public Works Department (PWD), Roads & Highway Department (RHD), Bridge Authority, and City Corporation play a vital role in this process. These departments depend on the advanced technology and expertise provided by ICONIC Engineering Ltd. to uphold the highest quality standards.
Rebar Location Assessment
Rebar location assessment refers to the process of determining the position, depth, and layout of reinforcement bars (rebars) within concrete structures without causing damage to the concrete itself. Non-destructive testing (NDT) methods such as the Profometer and ground penetrating radar (GPR) play essential roles in accurately locating reinforcement bars (rebars) within concrete structures.
The use of NDT methods for assessing rebar location, such as ground-penetrating radar (GPR) and electromagnetic methods, became more established in the 1970s and 1980s. These methods allowed for non-invasive evaluation of concrete structures to detect and locate rebar accurately. Notable contributions came from institutions like the American Concrete Institute (ACI) and the International Society for Concrete Repair (ISCR), which developed guidelines and standards for rebar assessment.
Rebar location assessment involves detecting and mapping the position, depth, and spacing of reinforcement bars embedded within concrete structures. This information is vital for structural analysis, renovation projects, and ensuring adherence to building codes.
The Profilometer, a widely used device for assessing the cover depth and location of rebar in concrete, was first introduced in the 1980s. It was developed by the Swiss company Proceq SA, which specializes in concrete testing equipment.
The initial concepts and prototypes for GPR were developed by researchers at the University of Kansas, including Dr. David A. P. McNeill and his colleagues, who adapted radar technology for subsurface exploration
Test Procedures with Profometer and Ground Penetrating Radar (GPR)
Profometer Test Procedure:
- Preparation: Ensure the concrete surface is clean and prepared for testing.
- Setup: Place the profilometer probe on the concrete surface at the desired location.
- Measurement: Conduct the following steps:
-
- Activate the profilometer to emit electromagnetic pulses into the concrete.
- Record and analyze the signals to detect the presence and position of rebars.
- Obtain measurements of rebar diameter, cover depth, and spacing.
Ground Penetrating Radar (GPR) Test Procedure:
- Preparation: Apply coupling gel to ensure good contact between the GPR antenna and the concrete surface.
- Setup: Move the GPR antenna systematically across the concrete surface.
- Scanning: Conduct the following steps:
-
- Transmit radar pulses into the concrete and record the reflected signals.
- Interpret the radar data to identify and map the location of rebars.
- Determine rebar depth, distribution, and potential anomalies within the concrete structure.
Advantages of Profometer and GPR
Profilometer:
- Accuracy: Provides precise measurements of rebar location, diameter, and cover depth.
- Versatility: Suitable for various concrete thicknesses and rebar configurations.
- Non-destructive: Does not damage the concrete or require intrusive methods.
Ground Penetrating Radar (GPR):
- Depth Penetration: This can penetrate deep into concrete to detect rebars at different depths.
- High Resolution: Offers detailed imaging of rebar layout and potential anomalies.
- Real-time Data: Provides immediate results for on-site decision-making.
Table showing some short parameters:
Aspect | Description |
Test Method | Rebar Location Assessment using Profometer and Ground Penetrating Radar (GPR) |
Purpose | Determine the precise location and depth of reinforcement bars (rebars) within concrete structures |
Methods | Profilometer (for cover meter assessment), GPR (for deeper penetration and detailed mapping) |
Advantages | Non-destructive, accurate rebar mapping, helps in structural integrity assessments |
Limitations | Surface conditions affect accuracy |
Common Failures:
- Accidental Damage: It can collapse damage in time of core drilling. Risk of unintentional damage to reinforcement during construction activities.
- Structural Weakness: Potential for inadequate reinforcement at critical points, compromising structural strength.
- Corrosion: Increased likelihood of corrosion due to insufficient concrete cover over rebars.
- Non-compliance: Failure to meet construction standards and regulatory requirements.
- Quality Issues: Construction defects and durability concerns in concrete structures.
- Safety Hazards: Risks of structural failure or collapse.
- Costly Repairs: Potential for expensive repairs and project delays.
Conducting rebar location assessments using appropriate methods is crucial to mitigate these risks and ensure the safety, durability, and compliance of concrete structures.
International Standards
These testing methods adhere to international standards to ensure reliability and consistency:
- ASTM C1060: Provides guidelines for measuring the thermal resistance (R-value) and thermal transmittance (U-value) of building materials, particularly insulation, using a guarded hot plate apparatus
- BS EN 1504-10: Products and systems for the protection and repair of concrete structures – Test methods – Determination of reinforcement corrosion – Profometer method.
Future Scopes Using These Technologies
The future of rebar location assessment with profilometer and GPR technologies holds several promising developments:
- Enhanced Resolution: Advancements in sensor technology for higher resolution and accuracy.
- Integration with AI: Use of artificial intelligence for automated interpretation and analysis of data.
- Online Applications: Development of apps for real-time data visualization and reporting.
- Environmental Adaptability: Improvement in devices to operate effectively in various environmental conditions.
In collaboration with entities such as the Local Government Engineering Department (LGED), Public Works Department (PWD), Roads & Highway Department (RHD), Bridge Authority, and City Corporation, regular maintenance and assessments of infrastructure and equipment are conducted. These collaborations enable the identification and resolution of potential issues before they become severe, with ICONIC Engineering Ltd.’s advanced technology and expertise ensuring that the highest quality standards are consistently achieved.
Rebar Corrosion Assessment
Rebar corrosion assessment involves evaluating the extent and severity of corrosion affecting reinforcement bars (rebars) within concrete structures. Non-destructive testing (NDT) methods, particularly the profilometer corrosion kit, play a critical role in detecting and assessing corrosion within reinforcement bars (rebars).
By the 1980s, electrochemical methods such as half-cell potential mapping became more commonly used to assess corrosion in concrete. Companies like Proceq SA developed and commercialized tools for detailed corrosion mapping and concrete condition assessment.
Rebar corrosion assessment involves identifying and evaluating the extent of corrosion within rebars embedded in concrete structures. Corrosion can weaken structures, compromising their safety and longevity, making timely assessment crucial for maintenance and rehabilitation.
The Half-Cell Potential Meter a widely used device for assessing the corrosion of rebar in concrete, was first introduced in the 1980s. It was developed by the Swiss company Proceq SA, which specializes in concrete testing equipment.
Test Procedure with Profometer Corrosion Kit
The profilometer corrosion kit integrates electrical resistivity measurements with rebar location capabilities to assess corrosion. Here’s a basic test procedure:
- Preparation: Ensure the concrete surface is clean, wet, and prepared for testing.
- Setup: Mix up the Sulphur powder with water and place it inside the corrosion kit. Place the profilometer probe on the concrete surface at the desired location.
- Measurement: Conduct the following steps:
-
- Roll on the profilometer to emit electromagnetic pulses into the concrete.
- Measure the electrical resistivity to assess the corrosive environment.
- Use the corrosion potential and half-cell potential measurements to detect corrosion activity.
- Obtain data on rebar diameter, cover depth, and spacing for corrosion assessment.
Advantages of Profometer Corrosion Kit
- Comprehensive Assessment: Provides combined rebar location and corrosion assessment in a single device.
- Non-destructive: Does not damage the concrete or require intrusive methods, minimizing disruption.
- Real-time Data: Offers immediate results for on-site decision-making and analysis.
- Accuracy: Delivers precise measurements of rebar corrosion potential and extent.
Table showing some short parameters:
Aspect | Description |
Test Method | Using Profometer Corrosion Kit |
Purpose | Evaluate the corrosion condition of reinforcement bars (rebars) within concrete structures |
Methods | Profometer Corrosion Kit (measures corrosion rate and potential) |
Advantages | Non-destructive provides quantitative corrosion data, guides maintenance decisions |
Limitations | Surface conditions affect accuracy |
Common Failures:
- Structural Weakness: Reduced load-bearing capacity and potential structural failure.
- Safety Risks: Hazards to occupants due to compromised structural integrity.
- Costly Repairs: Expensive repairs or replacements of corroded components.
- Durability Issues: Accelerated concrete deterioration and increased maintenance costs.
- Non-compliance: Violation of construction standards and regulatory requirements.
- Operational Disruptions: Disruptions to activities dependent on the structure.
- Environmental Impact: Potential hazards in industrial or hazardous environments.
Regular assessment using non-destructive testing methods is essential to mitigate these risks and ensure the safety and longevity of concrete structures.
International Standards
The profilometer corrosion kit adheres to international standards to ensure reliability and consistency in corrosion assessment:
- ASTM C876: Provides guidelines for measuring the corrosion potential of embedded reinforcing steel in concrete. This is done using a half-cell potential method to determine the likelihood of corrosion occurring.
- BS EN 1504-7: Products and systems for the protection and repair of concrete structures – Test methods – Determination of chloride content in hardened concrete and reinforcement corrosion potential.
Future Scopes Using This Technology
The future of rebar corrosion assessment with profilometer corrosion kits holds several promising developments:
- Advanced Sensor Technologies: Development of sensors for enhanced sensitivity and accuracy in detecting corrosion.
- Integration with Digital Platforms: Integration with digital tools for real-time data analysis, reporting, and predictive maintenance.
- Automation and AI: Use of artificial intelligence for automated interpretation of corrosion data and predictive modeling.
- Environmental Monitoring: Expansion into environmental monitoring to assess long-term corrosion risks.
Working together with the Local Government Engineering Department, Public Works Department, Roads & Highway Department, Bridge Authority, and City Corporation, regular check-ups on infrastructure and equipment are a breeze. ICONIC Engineering Ltd.’s top-notch technology and know-how, these groups can spot and fix any problems before they get out of hand.
Crack Assessment in NDT
Crack assessment is the process of inspecting, measuring, and analyzing cracks that develop in concrete, masonry, or other structural materials. Methods like ultrasonic pulse velocity (UPV) and ultrasonic pulse echo array play significant roles in detecting and characterizing cracks without causing damage.
Crack assessment began in the mid-20th century. Organizations like the American Concrete Institute (ACI) and the International Concrete Repair Institute (ICRI) published guidelines for assessing and repairing cracks in concrete structures. Assessment can be traced back to the development of ultrasonic testing technologies in the 1970s and 1980s.
Crack assessment involves identifying, locating, and evaluating cracks within concrete structures. Understanding the type and extent of cracks helps in determining appropriate repair and maintenance strategies to ensure structural safety and longevity.
Test Procedures with Ultrasonic Pulse Velocity (UPV) and Ultrasonic Pulse Echo Array
Ultrasonic Pulse Velocity (UPV) Test Procedure:
- Preparation: Ensure the concrete surface is clean and prepared for testing.
- Setup: Place ultrasonic transducers at specified locations on the concrete surface.
- Testing: Conduct the following steps:
- Transmit ultrasonic pulses into the concrete.
- Record the travel time of pulses and pulse velocity between transducers.
- Calculate the pulse velocity, which indicates concrete uniformity and the presence of cracks.
- Identify changes in velocity that may indicate crack locations and orientations.
Ultrasonic Pulse Echo Array Test Procedure:
- Preparation: Apply coupling gel for optimal contact between the transducer array and the concrete surface.
- Setup: Position the ultrasonic pulse-echo array systematically over the concrete area of interest.
- Scanning: Conduct the following steps:
-
- Transmit ultrasonic pulses and capture reflected signals from within the concrete.
- Generate detailed images and profiles of internal structures, including cracks.
- Analyze data to locate cracks, measure their dimensions, and assess their severity.
Types of Concrete Cracks
Concrete cracks can vary in type and characteristics:
- Structural Cracks: Result from overloading or structural deficiencies.
- Shrinkage Cracks: Form during the drying and curing process due to moisture loss.
- Settlement Cracks: Occur due to uneven settling or shifting of the foundation.
- Expansion Cracks: Arise from thermal expansion and contraction of concrete.
- Cracks Due to Corrosion: Result from reinforcement corrosion causing concrete cover cracking.
- Honeycomb: Honeycomb refers to voids or gaps left in concrete due to poor compaction or inadequate vibration during pouring. It appears as irregularly shaped holes or pockets within the hardened concrete.
Advantages of UPV and Ultrasonic Pulse Echo Array
UPV:
- Non-destructive: Does not damage the concrete during testing.
- Quick: Provides rapid assessment of concrete integrity.
- Quantitative Data: Offers measurable data on concrete quality and crack characteristics.
Ultrasonic Pulse Echo Array:
- Detailed Imaging: Provides high-resolution images of internal structures and cracks.
- Accurate Depth Measurement: Determines crack depth accurately.
- Versatility: Suitable for complex geometries and different concrete types.
Table showing some short parameters:
Aspect | Description |
Test Method | Crack Assessment using Ultrasonic Pulse Velocity and Ultrasonic Pulse Echo Array |
Purpose | Identify and evaluate cracks in concrete structures to assess structural integrity |
Methods | Ultrasonic Pulse Velocity device, Ultrasonic Pulse Echo Array |
Advantages | Non-destructive provides detailed imaging and analysis, helps in targeted repairs |
Limitations | Surface conditions affect accuracy |
Common Failures:
- Structural Weakness: Potential compromise of structural integrity over time.
- Water Damage: Increased risk of water ingress, leading to concrete deterioration and corrosion.
- Higher Repair Costs: Costly repairs and disruptions to project timelines.
- Aesthetic and Functional Issues: Decreased appearance and potential functional impairments.
Regular crack assessment is crucial to prevent these issues and ensure the safety and durability of concrete structures.
International Standards
These testing methods adhere to international standards to ensure accuracy and reliability:
- ASTM C597: Specifies procedures for measuring the ultrasonic pulse velocity in concrete to evaluate its quality and uniformity. This test through pulse velocity is useful for detecting internal defects such as voids and cracks and assessing the concrete’s overall condition.
- ASTM C1155: Standard Practice for Determining the Applicability of Groundwater Flow Models.
Future Scopes Using These Technologies
The future of crack assessment with UPV and ultrasonic pulse echo array technologies holds several promising developments:
- Enhanced Resolution: Improvements in sensor technology for higher resolution and accuracy in crack detection.
- Automation and AI: Integration with artificial intelligence for automated data analysis and predictive modeling of crack behavior.
- Real-time Monitoring: Development of sensors for continuous monitoring of crack propagation and structural health.
- Environmental Adaptability: Advancements in devices for effective operation in diverse environmental conditions.
In collaboration with entities such as the Local Government Engineering Department (LGED), Public Works Department (PWD), Roads & Highway Department (RHD), Bridge Authority, and City Corporation, regular maintenance and assessments of infrastructure and equipment are conducted. These collaborations enable the identification and resolution of potential issues before they become severe, with ICONIC Engineering Ltd.’s advanced technology and expertise ensuring that the highest quality standards are consistently achieved.
Minimum Cover Check & Assessment
The cover check involves measuring and verifying the thickness of the concrete cover protecting reinforcement bars embedded within concrete elements such as beams, columns, and slabs. The profilometer cover meter is a widely used tool for measuring the depth of concrete cover over reinforcement bars (rebars).
The American Concrete Institute (ACI) published various versions of its codes, including guidelines for concrete cover, starting with early documents in the mid-20th century. ACI 318, for example, has included cover requirements since its inception.
Minimum cover refers to the specified distance between the surface of the concrete and the embedded reinforcement bars. It is essential to prevent corrosion and maintain structural strength. NDT methods help ensure that these cover requirements are met without damaging the concrete.
Test Procedure with Profometer Cover Meter
- Preparation: Ensure the concrete surface is clean and prepared for testing.
- Setup: Place the profilometer probe on the concrete surface at the desired location.
- Measurement: Conduct the following steps:
-
- Activate the profilometer to emit electromagnetic pulses into the concrete.
- Measure and record the depth of the concrete cover over reinforcement bars.
- Obtain data on rebar diameter, spacing, and distribution.
Advantages of Profometer Cover Meter
- Accuracy: Provides precise measurements of concrete cover depth.
- Non-destructive: Does not damage the concrete or require intrusive methods.
- Speed: Offers rapid assessment of multiple locations on-site.
- Versatility: Suitable for various concrete thicknesses and rebar configurations.
Table showing some short parameters:
Aspect | Description |
Test Method | Minimum Cover Check using Profometer Cover Meter |
Purpose | Measure and ensure adequate thickness of concrete cover over reinforcement bars (rebars) |
Methods | Profometer Cover Meter (electromagnetic device for cover thickness measurement) |
Advantages | Non-destructive, precise measurement, ensures structural durability and safety |
Limitations | Surface conditions affect accuracy |
Common Failures:
- Corrosion Risk: Inadequate concrete cover exposes reinforcement bars (rebars) to moisture and environmental elements, increasing the risk of corrosion over time.
- Structural Weakness: Insufficient cover compromises the protective barrier around rebars, reducing their effectiveness in bearing loads and maintaining structural integrity.
- Durability Issues: Decreased durability of concrete structures due to early onset of corrosion and degradation of reinforcement.
Ensuring regular and accurate concrete cover checks using appropriate non-destructive testing methods is crucial to mitigate these risks, ensuring the longevity, safety, and compliance of concrete structures
International Standards
The profilometer cover meter adheres to international standards to ensure reliability and accuracy in minimum cover assessment:
- ASTM C174: Standard Test Method for Measuring Thickness of Concrete Elements Using Drilled Concrete Cores.
- BS EN 12504-2: Testing concrete in structures – Non-destructive testing – Determination of rebound number.
Future Scopes Using This Technology
The future of minimum cover assessment with profilometer cover meters holds several promising developments:
- Enhanced Sensitivity: Improvements in sensor technology for detecting smaller cover depths accurately.
- Integration with Digital Tools: Integration with digital platforms for real-time data analysis and reporting.
- Automation and AI: Use of artificial intelligence for automated interpretation of data and predictive maintenance.
- Environmental Adaptability: Development of devices suitable for various environmental conditions and concrete types.
Regular maintenance of infrastructure, done in partnership with LGED, PWD, RHD, the Bridge Authority, and the City Corporation, helps catch problems early. These organizations trust ICONIC Engineering Ltd. for the latest solutions and expertise to maintain top quality.
Penetration Testing
Penetration testing involves evaluating the ability of a material or structure to withstand penetration by water, air, chemicals, or other substances. The goal is to assess durability, resistance to environmental factors, and compliance with quality standards. Ultrasonic Pulse Velocity (UPV) is one of the techniques employed for penetration testing, particularly effective for assessing concrete structures.
1960s: The development of ultrasonic pulse velocity (UPV) and other ultrasonic methods began to gain traction in civil engineering for assessing concrete quality and structural integrity.
Test Procedure with Ultrasonic Pulse Velocity (UPV)
UPV is utilized to measure the velocity of ultrasonic pulses passing through concrete or other materials. The test procedure typically involves the following steps:
- Preparation: Ensure the surface of the material is clean and prepared for testing.
- Setup: Place ultrasonic transducers at specific locations on the surface of the material.
- Testing:
-
- Transmit Pulses: Send ultrasonic pulses through the material using one transducer.
- Receive Pulses: Capture the transmitted pulses with another transducer placed at a known distance.
- Calculate Velocity: Measure the time taken for the pulse to travel between transducers and calculate the pulse velocity using the formula: V=DTV = \frac{D}{T}V=TD, where VVV is the pulse velocity, DDD is the distance between transducers, and TTT is the time of flight of the pulse.
- Analysis: Interpret the results to assess the material’s integrity, including the presence of voids, cracks, or other defects.
Advantages of Ultrasonic Pulse Velocity (UPV)
- Non-destructive: Does not cause damage to the material under test.
- Quantitative Results: Provides measurable data on the material’s internal structure and integrity.
- Versatility: Applicable to various materials, including concrete, rock, and composites.
- Speed: Offers rapid assessment of large areas or multiple locations.
Table showing some short parameters:
Aspect | Description |
Test Method | Penetration Testing using Ultrasonic Pulse Velocity (UPV) |
Purpose | Evaluate the ability of concrete to resist penetration by fluids or chemicals |
Methods | Ultrasonic Pulse Velocity (UPV) device |
Advantages | Non-destructive provides quantitative data, assesses durability against environmental factors |
Limitations | Surface conditions affect accuracy, require calibration |
Common Failures:
- Water Ingress and Leakage: Without testing for water penetration resistance, structures may be susceptible to leaks and water damage, compromising durability and causing costly repairs.
- Air Permeability Issues: Lack of air permeability testing can result in energy inefficiency, poor indoor air quality, and discomfort for occupants.
- Chemical Resistance: Failure to assess chemical penetration resistance can lead to material degradation, corrosion, and compromised safety in chemical environments.
Ensuring thorough penetration testing using appropriate methods and standards is crucial to mitigate these risks, ensuring the durability, safety, and performance of construction projects.
International Standards
UPV testing adheres to international standards to ensure consistency and reliability in measurements:
- ASTM C597: Specifies the procedure for measuring the ultrasonic pulse velocity in concrete to assess its quality and uniformity.
- BS EN 12504-4: Specifies the procedures for determining the ultrasonic pulse velocity in concrete. This method helps evaluate the uniformity, quality, and integrity of concrete by measuring how quickly ultrasonic waves travel through it.
Future Scopes Using This Technology
The future of UPV technology in penetration testing includes several promising developments:
- Enhanced Accuracy: Improvements in sensor technology for higher accuracy in pulse velocity measurements.
- Integration with Digital Platforms: Incorporation of digital tools for real-time data analysis and reporting.
- Automation and AI: Use of artificial intelligence for automated interpretation of test results and predictive maintenance.
- Environmental Adaptability: Development of devices capable of operating in diverse environmental conditions and on complex geometries.
Working together with the Local Government Engineering Department, Public Works Department, Roads & Highway Department, Bridge Authority, and City Corporation, regular check-ups on infrastructure and equipment are a breeze. ICONIC Engineering Ltd.’s top-notch technology and know-how, these groups can spot and fix any problems before they get out of hand.
Subsurface Utility Locating & Mapping
Subsurface utility locating and mapping is a critical process in infrastructure development and maintenance, aiming to identify and map underground utilities and structures without excavation. Ground Penetrating Radar (GPR) is a key technology used for this purpose, providing non-destructive means to detect and visualize subsurface objects and utilities.
1950s-1960s: The practice of locating subsurface utilities began to evolve with the development of basic detection methods, including electromagnetic and ground-penetrating radar (GPR) technologies. Early methods often involved simple electromagnetic sensors and manual mapping techniques.
Subsurface utility locating and mapping involves identifying and mapping underground utilities such as pipes, cables, and other structures to prevent damage during excavation and construction activities. This helps in planning and executing projects safely and efficiently.
Test Procedure with Ground Penetrating Radar (GPR)
- Survey Planning: Plan the survey area and mark boundaries for data collection.
- Setup: Configure the GPR system with appropriate antennas and settings suitable for the survey depth and soil conditions.
- Data Collection:
-
- Data Acquisition: Move the GPR unit systematically across the survey area while collecting data continuously.
- Analysis: Real-time or post-processing analysis of radar signals to identify anomalies indicative of subsurface utilities or structures.
- Mapping: Generate 2D or 3D maps of subsurface utilities based on the radar data interpretation.
Advantages of Ground Penetrating Radar (GPR)
- Non-destructive: Does not require excavation or physical probing, minimizing disruption and damage.
- High Resolution: Provides detailed images of subsurface features, including utility pipes, cables, and voids.
- Versatility: Applicable to various soil types and conditions, from urban areas to remote locations.
- Real-time Data: Enables immediate decision-making during surveys with on-site data analysis capabilities.
Table showing some short parameters:
Aspect | Description |
Test Method | Subsurface Utility Locating & Mapping using Ground Penetrating Radar (GPR) |
Purpose | Identify and map underground utilities (water pipes, gas lines, electrical cables) for excavation safety and planning |
Methods | Ground Penetrating Radar (GPR) |
Advantages | Non-destructive provides accurate depth and location data, enhances safety during construction |
Limitations | Accuracy is affected by soil conditions and depth, skilled interpretation required, and wet conditions. |
Common Failures for Not Using GPR:
- Utility Damage: Without GPR, there’s a higher risk of accidentally damaging underground utilities like water pipes, electrical cables, or gas lines during excavation activities.
- Safety Risks: Inaccurate utility location increases the danger of safety incidents for workers and nearby residents due to unexpected utility strikes.
- Project Delays and Costs: Unforeseen utility strikes lead to delays, redesigns, and additional costs for repairing or rerouting damaged infrastructure, impacting project timelines and budgets.
- Service Disruptions: Disrupting essential services like water supply, electricity, or telecommunications due to utility strikes affects businesses, residents, and emergency services relying on these utilities.
- Reputation Damage: Incidents stemming from inadequate utility locating can tarnish the reputation of construction firms, impacting client trust and future project opportunities.
Using GPR for subsurface utility locating before excavation mitigates these risks by providing accurate utility maps, enhancing safety, ensuring regulatory compliance, and facilitating smooth project execution.
International Standards
Ground Penetrating Radar (GPR) for subsurface utility locating adheres to international standards to ensure reliability and consistency:
- ASTM D6432: Standard Guide for Using the Surface Ground Penetrating Radar Method for Subsurface Investigation.
- ISO 18674: Provides guidelines for conducting geohydraulic tests, which are used to assess the hydraulic properties of soil and rock. These tests are essential for understanding groundwater flow, soil permeability, and other hydraulic properties important for geotechnical engineering. Geotechnical investigation and testing- Geophysical testing — Part 1: Preamble and general requirements.
Future Scopes Using This Technology
The future of subsurface utility locating and mapping with GPR includes several advancements and potential applications:
- Advanced Data Interpretation: Integration with artificial intelligence for automated feature detection and classification.
- Miniaturization and Mobility: Development of compact and mobile GPR systems for easier deployment in diverse environments.
- Integration with GIS: Enhanced integration with Geographic Information Systems (GIS) for seamless mapping and data management.
- Multi-sensor Fusion: Fusion of GPR data with other sensing technologies for enhanced subsurface characterization and utility mapping accuracy.
Regular maintenance and inspections of infrastructure and equipment are critical to preventing issues from escalating. Collaborations with key stakeholders such as the Local Government Engineering Department (LGED), Public Works Department (PWD), Roads & Highway Department (RHD), Bridge Authority, and City Corporation play a vital role in this process. These departments depend on the advanced technology and expertise provided by ICONIC Engineering Ltd. to uphold the highest quality standards.
ICONIC Engineering Ltd. is a leader in providing comprehensive Civil NDT services in Bangladesh. Our expertise spans a wide range of critical assessments, including concrete compressive strength testing, concrete uniformity mapping, rebar location, rebar corrosion evaluation, crack assessment, and minimum cover checks. By employing cutting-edge technologies and adhering to international standards, we deliver accurate and reliable results that help our clients maintain structural integrity, ensure safety, and comply with regulatory requirements.
In the rapidly evolving construction landscape of Smart Bangladesh, the importance of reliable and precise NDT services cannot be overstated. ICONIC Engineering Ltd. is committed to supporting the nation’s infrastructure development by offering innovative NDT solutions that mitigate risks, prevent failures, and enhance the overall quality of construction projects.